Metals go from strength to strength
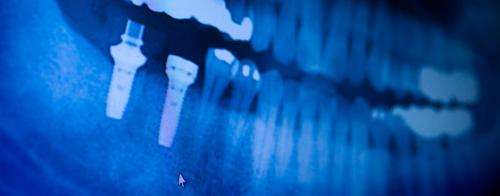
To the human hand, metal feels hard, but at the nanoscale it is surprisingly malleable. Push a lump of metal with brute force through a right-angle mould or die, and while it might look much the same to the naked eye when it comes out, the force applied to pressure it through the right-angle bend fundamentally changes its structure.
As a new nanostructuring technique, this is relatively simple, if somewhat brutal, says Professor Yuri Estrin, who is leading research into this technique at Monash University's Centre for Advanced Hybrid Materials.
The research is assessing the advances that can be achieved in a range of metals when subjected to this process – some anticipated, such as increased strength, others unexpected, such as greater corrosion resistance and increased biocompatibility.
"Metals are actually made of small crystallites, or grains," Professor Estrin says. "Applying mechanical load to deform the metal in specially designed processes breaks these into smaller and smaller fragments, down to a nanoscale granularity, while maintaining the material's overall structure."
The more times the metal is pushed through the die, the smaller the grains become; the smaller the grains, the stronger the material, although there is a natural limit to both the reduction in grain size and the improved strength.
Using this technique, or variations of it, often repeated many times, Professor Estrin and his principal co-researcher, Associate Professor Rimma Lapovok, increased the strength of titanium by up to 30 per cent. An even more spectacular increase – by a factor of eight – was achieved with pure copper.
"In metals that are already strong the potential for improvement is not as great, perhaps only 30 to 50 per cent," Professor Estrin says. "But if you can make a metal structure lighter by 30 to 50 per cent and maintain the same structural performance, this is certainly of interest to a wide range of industries."
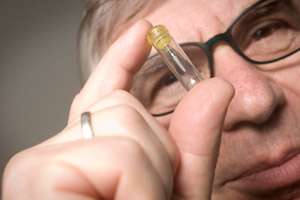
International collaboration
Professor Estrin and his team are already collaborating with the US-based specialty metal manufacturer Carpenter Technology Corporation, which produces ultra-fine-grain metals for biomedical implants. The Australian company Cochlear, an international leader in hearing implant technologies, is also involved in the research.
The collaboration with Carpenter Technology Corporation focuses on the potential of the enhanced titanium for dental implants. These take the form of titanium screws fixed into the jaw to hold artificial teeth, which have become a popular alternative to dentures in the past 15 years.
The screws are currently made of a titanium alloy that includes aluminium and vanadium to provide additional strength, but both elements are considered by some to be potentially toxic.
"Dental surgeons would like to have pure titanium. It is more biocompatible, but it doesn't have the strength of the alloy. However, we can take commercially pure titanium and use nanostructuring to give the material extra strength. This leaner, cleaner and stronger titanium compensates for the loss of the alloying elements."
Professor Estrin's enhanced titanium has the ability to withstand greater stress under cyclic loading – for example, the repeated application and release of loads common to actions such as chewing. A leading authority on dental reconstruction, Associate Professor Roy Judge, says improved metallurgy for implants would mean they lasted longer and would ultimately improve patient wellbeing.
Associate Professor Judge, who is head of prosthodontics at the Melbourne Dental School, says that while implant technology has advanced significantly over the past 15 years, there are ongoing issues with the loosening and fracture of implant screws.
"The load on the back teeth has been shown to be 50 to 80 kilograms, particularly for those who habitually grind their teeth. This application of high loads over prolonged periods has led to the failure of the implant screws, so improved fracture resistance would provide significant benefits for clients who sometimes struggle with the maintenance of their implants," he says.
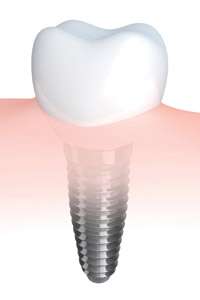
Resorbable implants
In related research, Professor Estrin is also developing magnesium for use in maxillofacial (face and jaw) surgery, to support broken bones and for vascular stents.
"There is huge interest in biodegradable or bio-resorbable implants that gradually dissolve during the healing process, reducing the risks of inflammation and eliminating the need for repeat surgeries to replace or remove implants. Magnesium is a prime candidate for such resorbable implants as it is entirely biocompatible – and many people actually have a magnesium deficiency."
However, magnesium can dissolve too fast. Professor Estrin is working with researchers in South Korea, Israel and Germany to control the dissolution rate of such nanomaterials for use in temporary implants. Just recently, Professor Estrin started a large collaborative project at the Moscow Institute of Steel and Alloys. Funded by the Russian Ministry of Education and Science, this project explores new approaches to bulk nanomaterials for biomedical applications.
Professor Estrin says while the nanostructuring techniques he works with are comparatively simple, he continues to discover possible ways of making materials more functional for a variety of purposes. Lighter, stronger metals are sought after in the automotive and aviation industries, as well as in biomedicine.
His search for enhancements extends from pure metals to alloys and to new hybrids that incorporate often dissimilar materials, such as metals and polymers.
"We have already shown that our process can improve the hydrogen storage capabilities of magnesium alloys – a property that can potentially be used in a future hydrogen economy," he says. "When we refine the structures to achieve ultra-fine crystallinity, new and interesting properties emerge, and existing properties can be improved."
Provided by Monash University